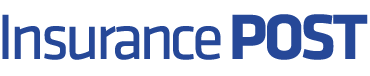
Spotlight: Sustainability: Modern methods of construction
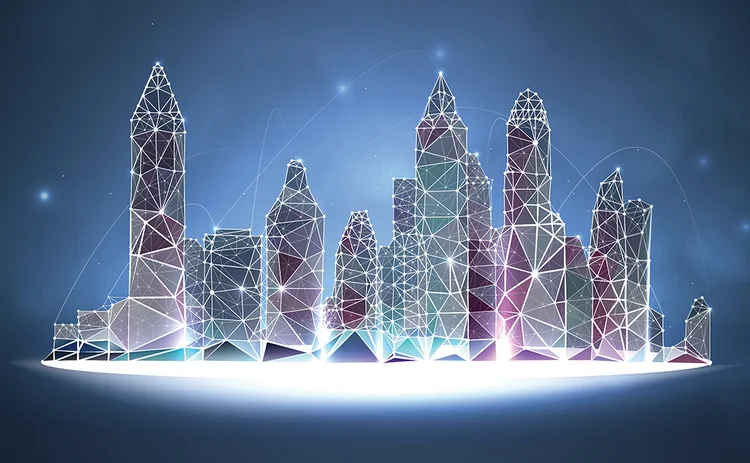
As the drive to a greener, more sustainable housing market continues so modern methods of construction are increasing in both popularity and usage. This drive is coming from a combination of government policies, consumer demand and also from within the industry itself
Earlier this year the Construction Leadership Council published a roadmap for the industry, which highlighted the increasing role of modern methods of construction to promote housing quality, zero carbon and resource efficiency and output and embed building safety considerations.
MMC fits firmly within the UK Government’s Construction 2025 plan to lower emissions and deliver projects faster and at a reduced cost. Funded as a direct result of the Construction Sector deal, the Construction Innovation Hub aims to transform the UK Construction sector by enabling and blending manufacturing technologies with digital methods of working efficiently.
In July Prime Minister Boris Johnson announced UK industry will receive around £350m to cut down carbon emissions under new plans to step up efforts to tackle climate change. This included £26m to support advanced new building techniques in order to reduce build costs and carbon emissions in the construction industry.
However, the push for a more sustainable construction sector also brings new challenges for insurers. Indications are that the landscape is set to change at a pace, potentially bringing heightened and new emerging risks.
Richard Forrest Smith, CEO of ECIC, part of Markel UK, which provides cover for contractors and trade associations across the engineering services sector, says: “Having the construction industry do their part for the environment by using green materials will help to hit the zero carbon emission targets set for 2050.
“However, this brings challenges, not least around the introduction of new building techniques. The insurance industry will experience issues resulting from the changes in technology. Products can come to the market before they are fully developed and, if training in new techniques is not as robust as it should be, unstable fittings and other issues can arise. Without the thorough training for renewable energy, push fit plastic joints and other innovations, we’ll see an increase in product fires, burst pipes and other claims.”
Competent design and build
Embracing appropriate and fully tested MMC with competent design and build should mean that traditional materials and methods continue to be used alongside newer and innovative options that are both resilient and sustainable.
Andy Miller, technical loss control manager at Allianz UK, says: “A key element when thinking about MMC construction is the approach to the building materials and how they interact with each other. From that point of view the materials and methods, whether traditional or modern, don’t always equate to a better or safer option.
“For example, exposed combustible materials in a finished structure present quite a different fire risk to those fully encapsulated in non-combustible or fire resistant materials.
“This is where realistic and ‘real world’ test standards have a crucial part to play to ensure MMC materials and systems are fit-for-purpose; an area that needs further scrutiny and development, alongside regulation so that safer buildings can be constructed keeping pace with the ever increasing speed of innovation in this area.”
Miller says that there is a common understanding of risk in traditional builds assisted by onsite flexibility during construction that can account for any imperfect site features or conditions.
He adds: “For modern methods where structures might be manufactured elsewhere offsite and then assembled onsite, the smallest deviation from factory perfect conditions can affect the structure in terms of the spread of fire/smoke, escape of water and weathering. Competency in satisfactorily correcting or adapting these imperfections is a key factor.
“It’s also worth considering the extent to which a building is considered ‘sustainable’. It’s not only about the materials used, but also the location and design and build, so that the building can stand the test of time, being resilient for example to fire, flood, EoW or storm events, as well as future proofed for our changing climate.”
As the construction and housebuilding sectors continue to change apace they face both heightened existing risks, as well as new emerging ones. Although MMC may be the answer to speed, cost and precision to combat the current housing crisis; the potential losses arising from a building constructed using MMC could be significant – particularly where the long term performance of modern materials is unknown.
Complete risk exposure
Joanne Foley, chief operations officer, global construction at Willis Towers Watson, says: “A genuine understanding of the complete risk exposure avoids gaps and enables the client to evolve their insurance covers, working with partners familiar with their business, to integrate specifics such as off-site exposures, manufacturing, product, completed operations and transit risks as well as supply chain and interdependency risks.
“This understanding should also encompass the benefits of deploying MMC to reduce risks associated with construction activity such as improved worker safety, cost and time efficiencies, increased accuracy on completion dates, less site disruption and defect minimisation. Through this culture of learning and understanding, the concerns which insurers will have around fire, durability, supply chain and technical skills are addressed more effectively.
“MMC is not new but as it becomes increasingly adopted, we have every confidence that our market will continue to evolve and provide the right solutions to our clients.
“However, they do require tailoring to avoid gaps in cover and as these techniques are more widely adopted the evolution of the market will need to continue. The current situation being experienced by all of us globally is a clear demonstration that assumptions regarding risk do not always materialise as initially perceived.”
Nevertheless, Colin Donnellon, development director at specialist construction broker Clear MPW, says: “There appears to be a lack of consistency across the market, with most insurers involved in construction insurance tending to prefer risks involving traditional building methods. Insurers remain nervous of non-traditional construction methods, as they are perceived to increase the potential fire risk during construction dramatically.
“History has shown there to be a number of high-value fire claims resulting from timber frame construction and other methods involving materials of a more combustible nature.”
Although existing insurance products can often meet these risks, sometimes multiple policies may have to be placed to insure the full supply chain risk; resulting in potential gaps or overlaps of cover.
Materials used
John Nicholls, product lead construction at insurer HSB, says: “The increased susceptibility to certain perils depends on the materials used, storage arrangements, efficiency and pedigree of the supply chain. The experience of the off-site components/module manufacturer determines whether there is an increased risk of repeated manufacturing errors leading to defects.
“The repetitive nature of the manufacturing process helps speed up project delivery times and also, with fine tuning, establish a high quality end product, by reducing defects. In addition the manufacturing environment will typically be less exposed to weather perils compared to the construction site.
“The storage of components and modules is another increased concern compared to raw materials. If the materials involved are combustible there is potentially a heightened fire risk although typically with the bulk of the manufacturing being done offsite the amount of hot works is generally reduced although the impact of a malicious fire is likely to be increased.
“The ingress of water can be a major issue unless adequate weatherproofing is put in place. There is potential for significant losses if rain seeps into and floods the structure before the contractor had a chance to make the units watertight. Monitoring weather conditions regularly and keeping unsealed units to a minimum can be an effective way to mitigate this risk.”
Larger sites and projects
As these risks continue to develop and are placed in the context of larger sites and projects it is possible that project insurance will become an increasingly commonplace solution as sharing the risk proves a better way of managing the risk.
Nicholls says: “The pursuit of positive change will inevitably encourage elements of construction that are prototypical in nature and which insurers often view with caution. But with the financing of projects reliant on insurance support, insurers will continue to play a critical role.
“Specific project insurance will be the natural choice for larger MMC projects and insurers have a large part to play in collaborating with the industry to support and encourage innovation.
“When insurers are engaged from the start, work collaboratively with the industry and potentially share the project risk among a number of insurers, we will inevitably see an increase in momentum, enthusiasm and drive to innovate.”
Donnellon agrees: “For those risks involving larger contract values, placement may need to be shared by more than one insurer. Additionally, some insurers have moved away from the annual construction business to focus on individual projects.
“The advantage being, underwriters will be in possession of the full facts relating not only to construction but health and safety, risk management, materials for incorporation and site protection information for the contract location. Annual construction policies tend not to demand the precise detail of every contract.
However, according to Donnellon, insurers need to understand the full facts of the risk being presented, and for the larger risk, the most effective way of understanding this is to present insurers with information on a contract-by-contract basis.
He adds: “Ultimately, contract site security is a key requirement to meet insurers risk acceptability criteria, and this may require 24-hour security, including alarm protection, depending on the contract value at risk.
“Premiums are likely to be more expensive along with higher levels of policy excess, and potentially more restrictive terms and conditions applying.
“An experienced construction insurance broker will build a detailed presentation of the risk to present insurers with the full facts, allowing them to underwrite with accuracy and ultimately provide the most favourable terms.”
The CLC road map makes specific mention about the availability of trade credit and professional indemnity insurance “to enable the industry to make best use of government support and access the insurance products required to support activity”.
However, these markets have been hardening for some time now, and continue to do so, with insurers reducing capacity or leaving them altogether.
Foley says: “The construction and in particular the PI insurance market continues to be challenging and the main constraint for MMC will be around fire risk. With concerns around cladding and broader fire safety at the forefront of PI insurer’s minds, we are seeing a continued restriction of cover in this area which we expect to continue to be challenging for our clients.”
On the other hand market withdrawals create space for other underwriters to step in and provide a much-needed service.
Rob Aston, senior underwriter at managing general agents Ensurance, says: “Contraction of providers simply creates opportunity for others. Prices may rise, and cover may tighten, which may restrict consumer choice, but available markets will not contract to the extent that certain construction approaches are considered unacceptable across the whole market. In a similar vein to that of timber frame construction, the core cover needed for MMC will continue to be available.”
Moving with the times
On the whole, it should also be recognised that MMC do not necessarily equate to a lower quality. Instead, it is essential to recognise that, like all sustainable industries, the building industry is simply moving with the times and evolving to serve the needs of its clients and wider society.
Miller concludes: “A good example of a traditional material that can be used effectively within modern construction is concrete. Whether used in a more traditional manner or innovatively such as 3D printing of building components and modules, or advances such as self-healing concrete using a dormant bacteria which activates to seal minor cracks that may appear, it’s clear that the industry is innovating and adapting.
“So, safety including appropriate test standards, context of materials and design and build competency are key factors when looking at sustainable and resilient modern methods of construction be they for residential or commercial use. The properties shouldn’t just be built in such a way that means the construction is zero carbon footprint for example, to be truly sustainable they need to be resilient for the long term.”
Only users who have a paid subscription or are part of a corporate subscription are able to print or copy content.
To access these options, along with all other subscription benefits, please contact info@postonline.co.uk or view our subscription options here: http://subscriptions.postonline.co.uk/subscribe
You are currently unable to print this content. Please contact info@postonline.co.uk to find out more.
You are currently unable to copy this content. Please contact info@postonline.co.uk to find out more.
Copyright Infopro Digital Limited. All rights reserved.
You may share this content using our article tools. Printing this content is for the sole use of the Authorised User (named subscriber), as outlined in our terms and conditions - https://www.infopro-insight.com/terms-conditions/insight-subscriptions/
If you would like to purchase additional rights please email info@postonline.co.uk
Copyright Infopro Digital Limited. All rights reserved.
You may share this content using our article tools. Copying this content is for the sole use of the Authorised User (named subscriber), as outlined in our terms and conditions - https://www.infopro-insight.com/terms-conditions/insight-subscriptions/
If you would like to purchase additional rights please email info@postonline.co.uk
Most read
- LV’s Mike Crane leaves insurer
- RSA ‘pragmatic’ on product review as NIG acquisition completes
- Wakam looking to exploit ‘unlimited UK potential’ following regulator approval