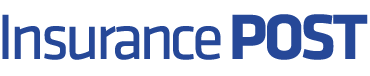
From farm to fork
As new European Union regulations look set to place more stringent requirements on food safety at each stage of the food production process, Adam Parsons stresses the importance of product recall insurance
The risk of having to recall a contaminated or defective product must be a major concern for any manufacturing company - products of one kind or another are recalled or withdrawn almost weekly in the
Only users who have a paid subscription or are part of a corporate subscription are able to print or copy content.
To access these options, along with all other subscription benefits, please contact info@postonline.co.uk or view our subscription options here: http://subscriptions.postonline.co.uk/subscribe
You are currently unable to print this content. Please contact info@postonline.co.uk to find out more.
You are currently unable to copy this content. Please contact info@postonline.co.uk to find out more.
Copyright Infopro Digital Limited. All rights reserved.
You may share this content using our article tools. Printing this content is for the sole use of the Authorised User (named subscriber), as outlined in our terms and conditions - https://www.infopro-insight.com/terms-conditions/insight-subscriptions/
If you would like to purchase additional rights please email info@postonline.co.uk
Copyright Infopro Digital Limited. All rights reserved.
You may share this content using our article tools. Copying this content is for the sole use of the Authorised User (named subscriber), as outlined in our terms and conditions - https://www.infopro-insight.com/terms-conditions/insight-subscriptions/
If you would like to purchase additional rights please email info@postonline.co.uk
Most read
- Esure offers customers six-months free cover for latest tech glitch
- LV’s Mike Crane leaves insurer
- Big Interview: Jason Storah, Aviva