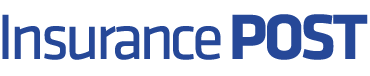
No more half measures
The UK lags behind the G7 by 13% in terms of productivity. Elizabeth Gooch says in order to bridge this gap, accepted ways of measuring productivity need improving
The government's central long-term economic objective is to achieve high and stable rates of economic growth and employment. Increasing productivity is the driving force behind this, and the route to
Only users who have a paid subscription or are part of a corporate subscription are able to print or copy content.
To access these options, along with all other subscription benefits, please contact info@postonline.co.uk or view our subscription options here: http://subscriptions.postonline.co.uk/subscribe
You are currently unable to print this content. Please contact info@postonline.co.uk to find out more.
You are currently unable to copy this content. Please contact info@postonline.co.uk to find out more.
Copyright Infopro Digital Limited. All rights reserved.
You may share this content using our article tools. Printing this content is for the sole use of the Authorised User (named subscriber), as outlined in our terms and conditions - https://www.infopro-insight.com/terms-conditions/insight-subscriptions/
If you would like to purchase additional rights please email info@postonline.co.uk
Copyright Infopro Digital Limited. All rights reserved.
You may share this content using our article tools. Copying this content is for the sole use of the Authorised User (named subscriber), as outlined in our terms and conditions - https://www.infopro-insight.com/terms-conditions/insight-subscriptions/
If you would like to purchase additional rights please email info@postonline.co.uk