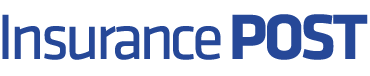
This article was funded by a third party, but the funder had no editorial control.
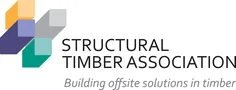
Spotlight: Sustainability - Driving down carbon emissions in the construction industry

Legislation passed in June 2019 requires the government to reduce the UK’s greenhouse gas emissions to net zero relative to 1990 levels by 2050. However, last December the Prime Minister Boris Johnson announced a new ambitious target to cut emissions by at least 68% by 2030 compared to 1990 levels. The UK’s new target – its nationally determined contribution under the Paris Climate Agreement – committed the UK to cutting emissions at the fastest rate of any major economy at the time.
Steel and concrete are among the worst producers of emissions, and so the construction industry needs to take action if the UK is to meet those targets. One way is to increase use of more sustainable materials like wood. Timber is currently the only construction material that captures CO2 from the atmosphere.
“For every cubic metre of timber used in construction, almost a tonne of CO2 is sucked in. Many of the trees used in the UK are grown in Scandinavia, which has extremely well managed forests. For every tree cut down, around five are planted. In fact, young trees take in more CO2 as they grow quicker than mature ones. We are not talking about construction consuming Amazonian hardwoods, or deforestation of tropical forests,” Andrew Orriss, Structured Timber Association’s Assure director explains.
However, insurance for timber construction is more expensive because there has been a general lack of experience and data as well as reassurance regarding the risks involved.
Campaigning for timber
Last July, the timber industry launched a ‘Wood CO2ts less’ campaign to encourage more wood use to reduce carbon emissions and fight climate change. The STA, an organisation representing the structural timber sector and associated supply chain companies also launched its ‘Time for Timber’ campaign last year.
The development of mass timber, a family of engineered wood products, including cross-laminated timber has helped drive up demand for wood in modern construction. These products are comprised of multiple solid wood panels nailed or glued together, which provide exceptional strength and stability. They are also made offsite.
Although used widely in other countries, structural timber construction has only recently taken off in the UK. It now accounts for over two-thirds of homes built in Scotland, while its use in England and Wales is accelerating.
“Housebuilders have embraced factory-build techniques over the past few years. Under pressure to increase output, they have turned to timber systems as it speeds up construction time and improves quality, giving them a much better rate of return,” Dave Hopkins, CEO of the Timber Trade Federation and the Confederation of Timber Industries’ lead says.
“In recent years developments in construction engineering have become so advantageous it makes sense to build using specialist engineered structural timber,” adds Oliver Novakovic, group technical and innovation director at Barratt Developments, the UK’s largest housebuilder.
Barratt aims to build 25% of its homes using modern methods of construction by 2025, of which structural timber makes up a large part. To ensure supply, Barratt purchased structural timber manufacturer Oregon Timber Frame in 2019.
Poor regulations
However, regulations are not keeping up with new methods of construction.
Allison Whittington, head of housing at Zurich, says: “We accept the government is under increased pressure to meet housing demand and net-zero targets and fully recognise that modern methods of construction, including the use of structural timber, are essential in helping tackle the housing crisis.”
“Further to Dame Judith Hackitt’s final report [a government review of building regulations and fire safety for high-rise residential buildings following the Grenfell Tower fire], it is clear the regulatory system is not fit-for-purpose, and Zurich would echo concerns there is a need for a radical rethink of the whole system and how it works. This is particularly evident for homes built using modern methods of construction and we are concerned by the absence of simple, clear baseline prescriptive standards. This is in contrast to growing evidence of severe impact on such constructions of events such as fire, flood or escape of water.”
Building taller
Mass timber is now starting to be used in large-scale public and commercial buildings. Currently, the world’s tallest timber building is the 18-storey Mjøstårnet by Voll Arkitekter in Norway, built using cross laminated timber.
Architect Andrew Waugh of Waugh Thistleton, which specialises in engineered timber buildings says: “Interest is growing in using timber for commercial buildings due to the ease and speed of construction, recognised health and wellbeing benefits, and investment value of being overtly carbon free.”
Waugh Thistleton is currently working on an office building made entirely with timber of just under half a million square foot in Milan and a 45,000 square foot one in London.
For now residential buildings using timber structures cannot exceed 18 metres in the UK.
According to Waugh: “There was a kneejerk change to regulations on the second anniversary of the Grenfell
tragedy which banned all combustible materials in the external walls of residential buildings over 18 metres. The Ministry of Housing, Communities and Local Government is well aware that banning mass timber was an unfortunate side effect of that new policy.”
“This means you have to replace a CLT wall which is six inches of solid material with light gage steel – which is a relatively flimsy external wall façade structure. It’s not a policy that anybody likes or wants, but was done quickly to meet the anniversary. The problem is it changes perception about existing buildings as well as new buildings.”
“Unfortunately everyone quotes Grenfell – and the irony is there was nothing remotely timber about Grenfell. Combustible phase change material cladding was the problem. Grenfell just shone a light on combustible materials in buildings, and timber is undoubtedly combustible,” comments Dominic Lyon, associate director at Gallagher.
Waugh adds: “The change in building regulations after Grenfell exempts PVC windows, for instance, but that is what melted and fell out and allowed the fire to spread. The one fireproof component at Grenfell were timber fire doors which didn’t fail in the fire.”
Quality control
Hopkins believes not enough has been done enough to inform the construction industry about building with timber. “I don’t consider it’s a material failure, rather a knowledge, skills and perception issue. It’s hard to get people to change the way they do things. And it’s difficult to build the skills base within contractors, which is getting harder following Brexit as much of their workforce comes from abroad.”
Orriss adds: “We applaud the new standards introduced post-Grenfell as it is about tackling the age-old problem of competency. The construction industry doesn’t have the same level of certification across all disciplines that exists, for example, in gas with Corgi-certified installers. To help improve quality in the structural timber industry, we created the STA Assure programme. So by choosing a STA member, you know they operate under that quality standard.”
To help ease insurers’ concerns, Gallagher has been working with the STA for several years. “Insurers have had reams of technical and best practice guidance for years. However, I don’t think the message of what the timber industry is doing is getting across sufficiently and the challenge is the effective articulation to insurers,” Lyon tells Post.
The Confederation of Timber Industries is developing guidance for the insurance sector to be known as the ‘Mass Timber Knowledge Hub.’ This year it will introduce an engagement and advocacy programme to engage more fully with insurers.

Comparative data
According to Tom Clapton, senior risk manager at QBE Europe: “There is enough data for conventional light timber construction in the UK to price risk. There is less data for buildings that use mass engineered timber elements, although there are UK examples of fires, such as the University of Nottingham’s in 2014 that informs insurers.”
Many insurers use data from their US offices. According to Phillip Callow, underwriter at Chase Underwriting International: “Within North America there is substantial data over many years which provides underwriters with a basis for pricing. Also, the volume of premiums within North America is significantly higher due to the long history of building with wood compared to the UK which provides a degree of ‘critical mass’”.
However, even in the US the adoption of engineered wood products is relatively recent. In January, Axa XL North America Construction launched a tailored Builders Risk insurance programme to specifically address mass timber project risks.
“A future of high-rise buildings using mass timber construction techniques is currently being discussed at the highest levels within insurance companies. The issues with light timber framing can be dealt with relatively simply through conditions and pricing as a means of describing risk appetite. High-rise buildings, however, are the properties of major portfolios and large clients – the stakes are high and risk of getting it wrong potentially catastrophic,” says Jim Glockling, director, Fire Protection Association/RISCAuthority.
Fire risk
Dave Clare, head of surveying services at loss adjusters Questgates comments: “Damage to timber can be much more widespread compared to steel and concrete, which, although not immune, do fare better when introduced to water escape or low-grade heat/fire. However, many new designs include solutions aimed at reducing spread, such as with sprinkler systems or de-oxidising environments.”
“Fire detection and property protection fire suppression systems would be required in a timber building,” adds Trevor Chainey, RSA’s UK construction practice lead, risk consulting. “The building regulations would only require life safety systems but this would be unlikely to satisfy insurers. This would require larger water tanks and more booster pumps in tall buildings making them more expensive to build.”
To reduce the risk presented by novel designs, it may be necessary to recognise the greater risk in the first place, and then substantially increase the use of large-scale testing that better reflects the actual conditions that will be experienced in service. Clapton explains: “The large-scale testing of common cladding systems as part of the Grenfell investigations showed that a number of these didn’t perform adequately and underscored how critical representative testing is.”
“It is very important structural timber buildings are made weathertight in the shortest time possible. During occupancy slow leaks from pipes can cause considerable damage so leak detection should be installed in all concealed areas. A timber building is likely to require more regular maintenance to ensure that no damp is penetrating the external envelope,” adds Chainey.
Reparability
According to Callow the inherent combustible nature of timber means that losses tend to be more severe if not total and understanding of reparability post event remains poor due to lack of experience and education.
He explains: “Project design should have reparability post event as a cornerstone not just for the construction but also for the operation of the project. Whereas traditional methods of construction are well known with longstanding and robust pricing models, insurers must assume a total loss scenario, which, combined with an unknown pipeline of premium, means pricing is more on feel and risk dynamics than on established models.”
From a liability perspective, structural timber buildings can pose concerns in so far as they continue to be considered as non-standard construction by many insurers. “Often structural timber forms the structural skeleton of a property and is often clad with typical standard construction material such as brick. This detail would generally only be visible to the trained eye and may not be common knowledge to the customer or broker taking out insurance, which can result in non-deliberate non-disclosure of key facts at proposal stage,” says Clare.
RISC Authority questionnaire
The RISC Authority has developed a questionnaire to illicit the information insurers need to make an informed insurance judgement. Namely, details of the consideration given to the protection of the building and the businesses conducted within it, and the mitigations proposed together with supporting evidence. It focuses on the known sensitivities of wood as a structural building material to the insurance perils of fire and water exposure.
“This has many advantages: the proposer quickly understands the insurance perspective, and they have a checklist of what they need to supply before conversations can continue, and even the scoring matrix the insurer will use during their review of the information supplied,” says Glockling.
Meanwhile, Whittington sees a wider issue: “Given the challenges with emerging technologies, we question whether it is appropriate to expect buildings to only offer a measurable degree of resilience beyond that of simply ensuring people can escape safely. Indeed, we have seen repeatedly examples of individuals, families, communities and businesses being displaced for significant periods following a peril event, resulting in significant non-financial impact.”
“With the unknown impact of climate change on the built environment, minimum standards must ensure greater levels of protection to be afforded as a matter of course. The additional benefits of designing to a property protection baseline is that the social and economic impact of peril events and climate change would be subsequently minimised.”
Sponsored
Copyright Infopro Digital Limited. All rights reserved.
As outlined in our terms and conditions, https://www.infopro-digital.com/terms-and-conditions/subscriptions/ (point 2.4), printing is limited to a single copy.
If you would like to purchase additional rights please email info@postonline.co.uk
Copyright Infopro Digital Limited. All rights reserved.
You may share this content using our article tools. As outlined in our terms and conditions, https://www.infopro-digital.com/terms-and-conditions/subscriptions/ (clause 2.4), an Authorised User may only make one copy of the materials for their own personal use. You must also comply with the restrictions in clause 2.5.
If you would like to purchase additional rights please email info@postonline.co.uk